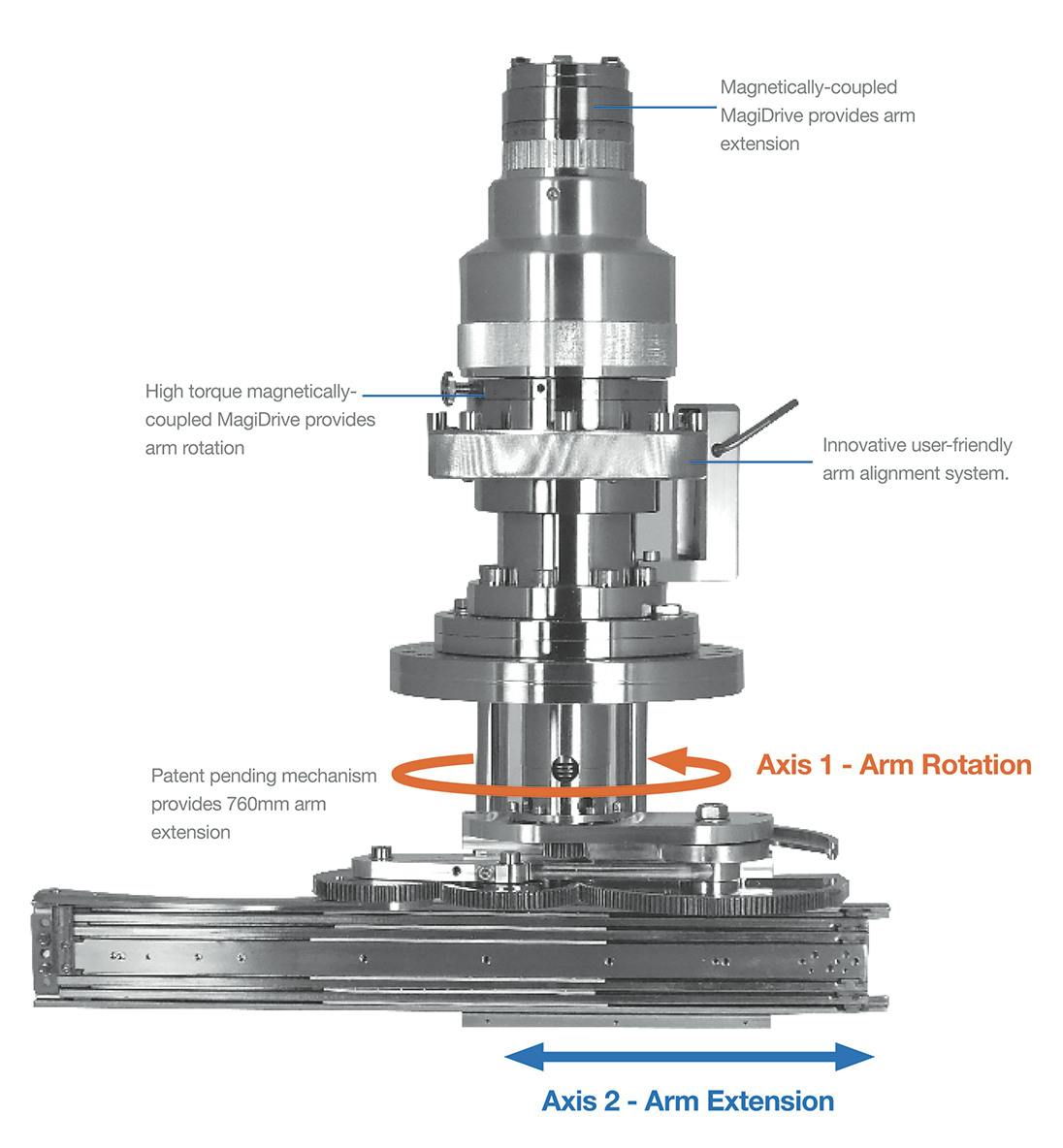
2-axis Rotary Telescopic Transfer Arm
360° rotation and 760mm linear extension
For preparation and analysis, radial systems require the precise transfer of samples between multiple chambers. This is handled from the central radial distribution chamber and it also uses a high torque magnetically-coupled MagiDrive to provide stiff coupling for radial motion. The innovative Radial Telescopic Transfer Arm (RTTA) offers unrivalled performance over conventional designs at comparable costs.
The RTTA is available in 2-axis and 3-axis versions
The manual version of the RTTA comes complete with an innovative, user-friendly system - designed to align the arm with the desired ports. A number of adjustable position stops are also fitted to the top of the thimble ring. These engage with a pair of spring-loaded bearings that can be withdrawn while the drive is rotated into position. They can then be re-engaged to hold the drive firmly in position via using a simple lever. What’s more, each stop can be individually aligned with a port axis to define default angular positions. These are highly reproducible.
True UHV rotation with no oil, slip rings, bellows or differential pumping. The Radial Telescopic Transfer Arm is actuated by the MD64LB and MD40 magnetically-coupled MagiDrive rotary feedthroughs. The larger MD64LB has a break-away torque of ~40Nm, providing an extremely stiff coupling. This makes it deal for rotating the arm assembly. The smaller MD40 actuates the mechanisms to drive the arm in and out.
Many radial distribution chambers system designs have an issue where the rotating arm motion causes the arm extension assembly to move (often described as the axis cross-talk). Consequently, this arm rotation causes the sample to be driven in and out - losing its position. Complex software programming is then required to unwind the secondary drive during arm rotation. At UHV Design, we’ve removed this issue via a unique mechanical design of tried-and-tested manipulators. These work by linking the rotary motion of the MD64 arm to the motor mounting of the smaller MD40. This mechanically unwinds the undesired motion - without the need for complex software.
If you would like to discuss your project with our engineering team, please contact us.